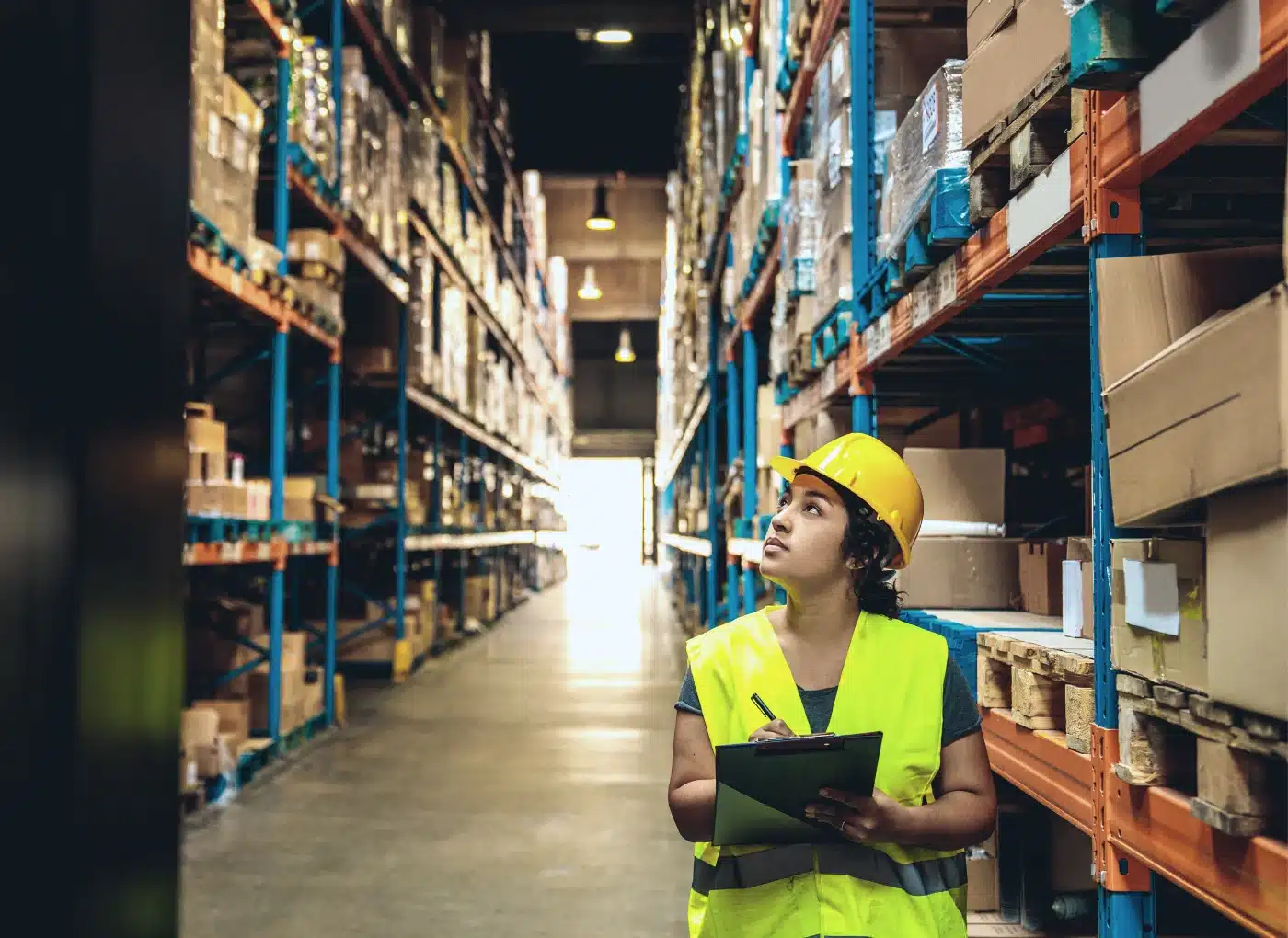
In the fast-paced world of warehouse operations, single-order (also known as discrete picking) picking remains a commonly used order picking strategy. While this method offers several benefits, including reduced errors and faster processing times, it also presents its own set of unique challenges. This article will delve into the intricacies of single-order picking, examine its potential inefficiencies and physical demands, and explore the role of strategic planning and innovative technologies in overcoming these hurdles. Whether you’re a seasoned warehouse manager or just starting in the industry, we will provide you with valuable insights to optimize your single-order picking process and boost your operational efficiency.
What is Single-Order Picking?
Single-order picking is an order picking method used in warehouse operations where a worker fulfills one customer order at a time. This process involves several steps:
- The worker receives a list of items for a specific order.
- They then move through the warehouse, picking each item from its storage location.
- Once all items are collected, they pack and prepare the order for shipment.
This method is straightforward and easy to understand, making it a preferred choice, especially for businesses new to order picking.
Comparatively, single-order picking has some unique features that differentiate it from other picking methods:
- Precision: Unlike batch or cluster picking where multiple orders are processed simultaneously, single order picking focuses on one order at a time. This reduces the risk of errors and ensures each order is accurately fulfilled.
- Speed: Since each order is processed individually, it allows for immediate packaging and shipment once an order is complete. This can lead to quicker delivery times and higher customer satisfaction.
- Simplicity: Other methods like zone or wave picking require more complex coordination and can be harder to manage. In contrast, single-order picking is simpler and easier to implement, especially for smaller operations or those with a wide range of SKUs.
Advantages of Single Order Picking
Reduced Errors
One of the significant advantages of single-order picking is its potential to reduce errors in the fulfillment process. Because pickers are focusing on one order at a time, they’re less likely to mix up items between orders. This precision leads to several benefits:
- Accuracy: Each order is fulfilled exactly as requested, leading to fewer returns or complaints.
- Customer Satisfaction: Accurate orders mean happy customers. This can lead to repeat business and positive reviews with fewer human errors.
- Efficiency: Less time spent correcting mistakes means more time for fulfilling new orders.
Easy to Learn/Train and Scalable
Another significant advantage of single-order picking is its simplicity and scalability:
- Easy to Learn/Train: Single-order picking is straightforward, making it easy for new employees to learn and master. This reduces the need for extensive training and allows for faster onboarding of new staff.
- Scalability: Single-order picking can easily scale to accommodate increased order volumes as your business grows. This flexibility makes it a sustainable choice for both small businesses and larger operations.
With its focus on accuracy and speed, single order picking can be a powerful tool in enhancing warehouse operations and improving customer satisfaction. However, like all methods, it comes with its own set of challenges.
IV. Challenges of Single-Order Picking
While single-order picking has its advantages, it’s important to also acknowledge the potential challenges that may arise with this method.
Potential Inefficiencies
One major caveat of single-order picking is that it can be inefficient, especially for larger operations. The reasons for these inefficiencies include:
- Travel Time: Because pickers must complete one order before moving on to the next, they may have to traverse the warehouse multiple times rather than picking multiple items in one pass leading.
- Downtime Between Orders: There can be a significant amount of downtime between orders, particularly if the picker has to return to a central location to receive the next order.
Physical Demands
Single-order picking can also be physically demanding for workers, particularly in large warehouses. This is due to:
- Increased Physical Activity: With more travel time comes increased physical activity, which can lead to worker fatigue.
- Greater Risk of Injury: The increased movement and handling of goods could potentially lead to a higher risk of injury.
Despite these challenges, strategic planning and the use of technology can help overcome these hurdles.
Strategies to Optimize Single-Order Picking
To maximize the benefits and minimize the challenges of single order picking, strategic planning, and the use of technology are key. Here are some suggestions to optimize this method:
Intelligent Warehouse Layout Design
An efficient warehouse layout can significantly reduce the travel distance for pickers, enhancing productivity and reducing physical strain. Here’s how:
- Locate High-Demand Items Near Packing Area: Positioning frequently picked items near the packing area can reduce travel time.
- Use a Logical Order for SKU Placement: Group similar items together and follow a logical sequence for item placement. This can make it easier for pickers to locate items quickly.
- Regularly Review and Update Layout: As demand patterns change, the warehouse layout should be reviewed and updated regularly to maintain efficiency.
Implementing Warehouse Management Systems (WMS)
A WMS can be a game-changer when it comes to improving efficiency and accuracy in single-order picking:
- Efficient Route Planning: A WMS can provide pickers with the most efficient route to collect items, minimizing travel time.
- Real-Time Inventory Tracking: With a WMS, inventory levels are updated in real-time, reducing the risk of overstocking or understocking issues.
- Data Analysis: A WMS can analyze picking data to identify trends and areas for improvement.
Using Robotics and Automation
Robotic systems can assist or replace human pickers, increasing efficiency and reducing the physical demands of single-order picking:
- Automated Guided Vehicles (AGVs): AGVs can transport goods within the warehouse, reducing the physical strain on workers.
- Picking Robots (AMRs): Picking Robots (AMRs) can pick items from shelves, increasing accuracy and productivity.
- Automated Storage and Retrieval Systems (ASRS): These systems store and retrieve items automatically, reducing the need for human intervention.
While single order picking has its challenges, with the right strategies and technology, it can be an effective method for many warehouse operations.
Final Thoughts
Single-order picking offers significant advantages like reduced errors and immediate processing and shipment, contributing to improved customer satisfaction. However, it also comes with its own set of challenges, such as potential inefficiencies and increased physical demands on workers. By implementing strategic planning in warehouse layout design and utilizing advancements in warehouse management systems or robotics, these challenges can be effectively addressed. Ultimately, the decision to use single-order picking should be based on an individual company’s needs, resources, and operational goals. With the right approach and tools, single-order picking can serve as a powerful strategy for enhancing warehouse operations and delivering superior service to customers.