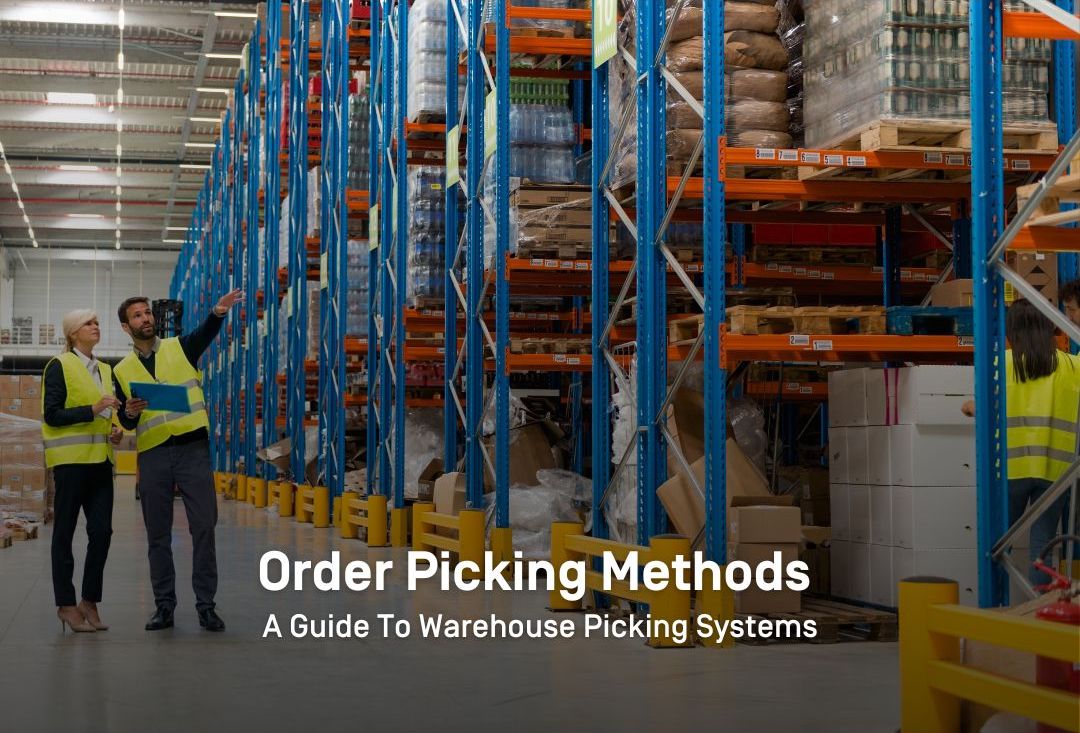
Efficient order-picking is the secret sauce for a well-performing warehouse, making sure orders are spot on and customer satisfied with their timely delivery. This guide is your backstage pass into the world of order-picking systems – each with its unique specifications, benefits, and potential challenges.
We’re here to show you how single-order picking, batch picking, zone picking, wave picking, and cluster picking, we will explain how these systems can optimize warehouse operations, reduce operational costs, and enhance customer service.Let’s dive in and make your warehouse the star of the show!
Different Types of Order-Picking Methods
Single Order Picking
Single order picking, often known as discrete picking, is commonly employed in warehouses and distribution centers. In this approach, workers pick one order at a time following a list of items for each order – called a pick list. These items are then packed and prepared for shipping before moving onto the next order. While this is a simple and straightforward approach, it might not be the most efficient method in operations with a high volume of orders, as it involves considerable travel time within the warehouse.
Single Order Picking Advantages
- Ease of Implementation: Single order picking is a straightforward method that doesn’t require complex systems or sophisticated technology. As such, it is easy to implement, making it suitable for small businesses or warehouses just getting started.
- Order Accuracy: Since orders are picked individually, the chances of errors are significantly reduced. This high level of accuracy can lead to better customer satisfaction.
- Flexibility: Single order picking is adaptable to a variety of warehouse layouts and product types. It allows for easy adaptation to changes in order volumes or product assortments.
- Minimal Training: Due to its simplicity, new or temporary staff can be quickly trained on single order picking, making it an ideal choice during peak seasons when extra hands are needed.
Single Order Picking Disadvantages
- Inefficiency in Large-Scale Operations: This method can be time-consuming in large-scale operations due to the high travel time between picks, potentially reducing productivity.
- Higher Operational Costs: May lead to higher operational costs, especially in larger warehouses, due to the increased time and labor involved in processing individual orders.
- Dependence on Skilled Workers: Although minimal training is needed, the effectiveness and efficiency of single order picking largely rely on the experience and skills of the workers. Errors can occur if the workers are not detail-oriented and meticulous.
- Difficulty in Handling Bulk Orders: Single order picking can be challenging when handling large, complex orders, as each pick requires individual attention, which can slow down the overall picking process.
- Increased Wear and Tear: The increased travel time impacts efficiency and causes more wear and tear on people and equipment.
Ideal Scenarios for Single Order Picking Use
- Small Warehouses or Businesses: As it doesn’t require complex systems or sophisticated technology, single order picking is ideal for small-scale operations where the volume of orders is manageable and the warehouse size doesn’t result in significant travel time.
- Operations with High Value or Sensitive Items: In operations where the products are high value or sensitive, the individualized attention of single order picking can ensure accurate and careful handling of every item.
- Variable Stock Levels and Products: If product types and stock levels frequently vary, the flexibility of single order picking allows for easy adaptation to these changes.
- Seasonal Peak Periods: During seasonal peaks when temporary staff are hired, the ease of training in single order picking can be beneficial in quickly getting the new staff up to speed.
- Businesses Prioritizing Customer Satisfaction: Businesses prioritizing high accuracy and customer satisfaction may prefer the single order picking method to minimize human errors and enhance their service quality.
Batch Picking
Batch Picking Advantages
- Efficiency: Reduces time spent traveling in the warehouse since pickers collect items for multiple orders in one pass. This time-saving advantage significantly increases productivity, especially in large-scale operations.
- Cost-Effective: By reducing the time order pickers spend walking or driving between picks, batch picking can help cut labor costs and minimize wear and tear on equipment, resulting in lower operational costs over time.
- Scalable: Scalable method that can handle an increase in order volume effectively. It is particularly useful during peak seasons or periods of rapid business growth.
- Improved Space Utilization: Since pickers are picking for multiple orders at once, products that are in high demand (and thus, often located in the same area) can be picked in one go, improving the utilization of warehouse space.
Batch Picking Disadvantages
- Increased Complexity: Unlike single order picking, batch picking involves the handling of multiple orders simultaneously which can increase the complexity of the picking process. This requires a higher level of organization and management to avoid errors.
- Need for Advanced Systems: Usually requires the use of more sophisticated systems or technology for order tracking, sorting, and packing. This means higher setup costs and the need for technical know-how.
- Risk of Errors: While this method can improve efficiency, it can also raise the risk of order errors since pickers are dealing with multiple orders concurrently. Any mistakes made during the picking, sorting, or packing stages can lead to customer dissatisfaction and potential returns.
- Training Requirements: The increased complexity necessitates comprehensive training for staff. This could mean additional time and costs spent training new or temporary workers.
- Dependency on Warehouse Layout: The efficiency is largely dependent on the warehouse layout. If the layout is not optimized for this method, it could lead to inefficiency and reduced productivity.
Ideal Scenarios for Batch Order Picking Use
- Large-scale Operations: Batch picking is particularly advantageous in large warehouses where travel time for picking individual orders could significantly impact productivity. By picking multiple orders at once, this method can save time and increase efficiency.
- Businesses with High Order Volume: For businesses that process high volumes of orders, batch picking helps to expedite the picking process and accommodate the influx of orders more effectively than single order picking.
- Operations with Commonly Ordered Items: If certain items are often ordered together or are in high demand, batch picking allows for the efficient collection of these items in one pass, improving the utilization of warehouse space.
- Peak Periods: During peak seasons or promotional events when order volume spikes, the scalability of batch picking can help manage the increased demand without the need for proportional increases in staff or resources.
- Businesses Prioritizing Operational Efficiency: For businesses aiming to streamline their processes and cut operational costs, the time and cost savings associated with batch picking can make it an attractive method. However, they must also be prepared to invest in training and advanced systems to handle the increased complexity.
Zone Picking
Zone Picking Advantages
- Enhanced Efficiency: Zone picking minimizes unnecessary movement, as pickers are confined to their specific zones, reducing travel time and increasing the speed of the picking process. This efficiency is particularly beneficial in large warehouses where items can be spread out over significant distances.
- Expertise Development: By consistently working in the same zone, pickers can gain a thorough knowledge of their assigned area and the products within it. This familiarity can lead to faster picking times and fewer picking errors.
- Streamlined Processes: Allows different orders to be processed simultaneously in separate zones. This parallel operation can significantly speed up order fulfillment times.
- Lowered Training Time: Training new employees can be quicker and more focused, as each picker only needs to become familiar with one area of the warehouse and its products.
- Flexibility: Can be easily adapted to both high and low demand situations. In high demand periods, more pickers can be assigned to each zone to increase picking speed. In lower demand periods, fewer pickers may be required, helping to manage labor costs.
Zone Picking Disadvantages
- Dependence on Effective Coordination: Requires seamless coordination between different zones. Any lapse in communication or a breakdown in the passing process can lead to delayed orders or errors.
- Limited Flexibility: This method may not be as flexible in handling sudden changes in order types or volumes. For instance, if one zone’s items suddenly become more popular, it could create a bottleneck in the picking process.
- Complex Order Management: Managing orders across multiple zones can be complicated, requiring a sophisticated order management system. This can increase operational complexity and require heavy initial investment.
- Training and Management:Despite reduced training times for individual zones, managing a workforce divided into different zones can be challenging and may require more advanced management skills.
- Unequal Workload Distribution: If not properly managed, some zones might end up with more workload than others, causing inefficiency and potential delays.
Ideal Scenarios for Zone Picking Use
- Warehouses with Large Product Variety: If an operation has a diverse range of items, dividing the warehouse into zones can allow pickers to become experts of their specific zone’s products. This can lead to reduced errors and improved picking efficiency.
- High-Volume Businesses: Zone picking is beneficial for operations that process a high volume of orders. The ability to process different orders simultaneously in separate zones can significantly speed up order fulfillment times.
- Businesses with Large Warehouses: In large warehouse environments where items can be spread out, zone picking minimizes unnecessary movement. By restricting pickers to their specific zones, travel time is reduced and the speed of the picking process is increased.
- Operations with Regular Order Profiles: If an operation often receives orders with items from the same zones, zone picking can be an efficient strategy. It allows for faster fulfillment of these orders as pickers become familiar with the common combinations.
- Peak Periods: During seasonal peaks or promotional periods when order volume spikes, zone picking can be scaled to manage the increased demand. More pickers can be assigned to each zone to speed up the picking process without needing an overall increase in resources.
Wave Picking
Wave picking is another order picking strategy that is often employed in warehousing operations to streamline the order fulfillment process. In this method, rather than being assigned to specific zones, pickers are given the freedom to move throughout the warehouse to gather all the items for a group of orders in a single pass. These orders are grouped or “waved” together based on certain shared characteristics, such as destination, carrier, or delivery route.
Wave Picking Advantages
- Increased Picking Speed: One of the primary advantages of wave picking is the increased speed of the picking operation. As orders are grouped together, pickers can gather all items needed for a wave of orders in one pass, reducing the time spent on unnecessary travel within the warehouse.
- Flexible Sequencing: Allows for flexible sequencing of the picking operations based on the characteristics of the order, like shipping time, carrier, or type of goods. This flexibility can improve warehouse workflow and optimize the order fulfillment process.
- Reduced Sorting Time: As orders are grouped together based on specific criteria, the sorting time of items after picking is significantly reduced. This can streamline the packing and shipping process, further improving efficiency.
- Compatible with Automated Systems: Highly compatible with automated picking systems, which can further enhance efficiency and accuracy. It can be integrated with warehouse management systems (WMS) for optimized order grouping and sequencing.
- Better Labor Utilization: Can lead to better utilization of labor resources. By scheduling waves based on labor availability, businesses can ensure a balanced workload and maintain consistent productivity.
Wave Picking Disadvantages
- Complexity in Order Consolidation: Involves the collection of items for multiple orders in one pass, which can lead to complex sorting and order consolidation processes. Failure to effectively consolidate orders can lead to errors and delays in order fulfillment.
- Increased Travel Time: Unlike zone picking, wave picking requires pickers to move throughout the warehouse. This can increase travel time and potentially reduce picking efficiency, particularly in larger warehouse settings.
- Inventory Management Challenges: Tracking inventory can be more difficult with wave picking, as items are picked in bulk for multiple orders. This can increase the risk of inventory errors and miscounts.
- Dependency on Technology: While wave picking can be made more effective with automation and advanced warehouse management systems, it also increases dependency on these technologies. Any technological failure or system downtime can significantly impact the picking process.
- Training Requirements: Requires pickers to be familiar with all areas of the warehouse and all types of products. This can increase the need for comprehensive training and ongoing skills development.
Ideal Scenarios for Wave Picking Use
- High-Volume Operations: Can be an effective strategy for businesses that process a large number of orders. By grouping orders based on shared characteristics, the efficiency and speed of picking can be improved, making it ideal for high-volume operations.
- Warehouses with Diverse Product Range: If a warehouse stocks a wide range of products, wave picking can be beneficial. By allowing pickers to move across different zones during a single picking cycle, it can enhance the efficiency of picking diverse items for a wave of orders.
- Operations with Varied Order Profiles: If the operation regularly receives orders that require items from various zones of the warehouse, wave picking can provide an efficient solution. It enables pickers to collect all items for a group of orders in a single pass, reducing the time spent on unnecessary travel.
- Businesses with Regular Shifts: Can be scheduled based on labor availability, making it a suitable option for businesses with regular shifts. It ensures a balanced workload and maintains consistent productivity, thereby optimizing labor utilization.
- Advanced Tech-Enabled Warehouses: Highly compatible with automated picking systems and warehouse management systems (WMS). If a warehouse operation has advanced technologies, wave picking can be incorporated to further enhance efficiency and accuracy.
- Seasonal Peaks or Promotional Periods: Can be scaled to manage increased demand during peak periods or promotional campaigns. By grouping orders into waves, more orders can be processed simultaneously, helping to handle volume spikes efficiently.
Cluster Picking
In a typical cluster picking operation, orders are grouped into clusters based on certain criteria such as delivery route or order characteristics. The picker then moves through the warehouse with a multi-compartment cart designed to hold all the items for the respective orders in the cluster. As the picker travels through the warehouse, they pick the items needed for all the orders in the cluster at once, depositing them into the appropriate compartments on the cart.
Cluster Picking Advantages
- Reduced Travel Time: As pickers fulfill multiple orders in a single pass, cluster picking minimizes warehouse travel time, improving efficiency and productivity.
- Increased Picking Accuracy: With a well-organized multi-compartment cart, pickers can easily match picked items to the correct orders, reducing the risk of errors and improving accuracy.
- Enhanced Order Processing Speed: By consolidating orders into clusters, more orders can be processed simultaneously, which can significantly speed up the order fulfillment process.
- Flexibility: Cluster picking is adaptable to different types of inventory and warehouse layouts, providing flexibility to meet the varying demands of order profiles.
- Cost-Effective: As it reduces travel time and increases order processing speed, cluster picking can lead to significant cost savings in labor and operational expenses.
Cluster Picking Disadvantages
- Complexity of Order Sorting: After picking, each order within the cluster must be sorted and packed separately. This process can be time-consuming, especially if not managed properly.
- Dependence on Warehouse Layout: The effectiveness of cluster picking largely depends on the warehouse layout. A poorly designed or unorganized warehouse can reduce the efficiency gains from cluster picking.
- Requires Investment in Specific Equipment: Often requires the use of multi-compartment carts or totes. This means additional investment in picking equipment, which may not be feasible for smaller operations.
- High Training Needs: The complexity of picking multiple orders simultaneously requires comprehensive training for pickers to minimize errors.
- Risk of Errors: As pickers are handling multiple orders at once, there can be an increased risk of errors such as mixing up items for different orders.
- Reliance on Technology: To effectively cluster orders, advanced warehouse management systems (WMS) or software may be necessary. This dependence on technology introduces the risk of operational disruption in the event of technical failures.
Ideal Scenarios for Use
- High-Volume Operations: Cluster picking is particularly useful in warehouses that process a significant number of orders. By picking items for multiple orders at once, it can greatly improve the efficiency and productivity of high-volume operations.
- Operations with Smaller Items: This method can also be beneficial in warehouses that primarily deal with smaller items. As these items can easily fit into the compartments of a multi-compartment cart, cluster picking can streamline the order fulfillment process.
- Businesses with Diverse Order Profiles: If a business regularly receives orders that require items from various zones of the warehouse, cluster picking can be an efficient solution. It allows pickers to pick items for multiple orders in a single pass, reducing unnecessary travel time.
- Warehouses with Regular Shifts: Can be scheduled based on labor availability, making it a suitable option for operations with regular shifts. It ensures a balanced workload, maintains consistent productivity, and optimizes labor utilization.
- Tech-Enabled Warehouses: Cluster picking requires an effective warehouse management system (WMS) or equivalent software to cluster orders effectively. As such, it is an ideal method for warehouses with advanced technological capabilities.
- Peak or Promotional Periods: Like wave picking, cluster picking can also be scaled to manage increased demand during peak periods or promotional campaigns. By grouping orders into clusters, more orders can be processed simultaneously, helping to handle volume spikes efficiently.
Use of Technology in Order Picking
- Barcode Scanners: These tools help in quick identification of items, thus reducing the manual search time and speeding up the warehouse picking process.
- Voice-Directed Picking Systems: These systems use voice prompts to guide workers through their tasks, enhancing speed and minimizing errors.
- Pick-to-Light Systems: By using visual cues to indicate the pick location of items to be picked, these systems simplify the process and decrease the likelihood of mistakes.
- Pick-To-Color Systems: inVia Robotics user-friendly software with a color-based interface directs warehouse workers to efficiently handle goods in the order process, tripling productivity rates.
- Autonomous Mobile Robots (AMRs): Autonomous mobile robots are material-handling robots that navigate autonomously in the warehouse. There are many different AMRs on the market today, including Person-to-Goods smartcarts, Rack-to-Person mobile robots and inVia Robotics Totes-to-PickerWall robots.
- AGVs: Automated Guided Vehicles (AGVs) are a type of robot that can navigate and transport goods throughout the warehouse through a pre-defined track.
- Vertical Lift Modules (VLMs): VLMs are automated storage and retrieval systems that deliver items to an operator at an ergonomically safe and convenient access point. They increase storage density and improve picking accuracy.
- AS/RS: Automated Storage and Retrieval Systems (AS/RS) are automated systems that store and retrieve goods, which helps to improve inventory accuracy, reduce labor costs, and optimize storage space.
- Robotic Palletizing: Robotic palletizing is a type of automation used in warehouses to help with the efficient loading and unloading of products into or out of pallets.
In conclusion, the choice of order picking methods is pivotal in determining the effectiveness and efficiency of warehouse operations. Each method, be it piece picking, batch picking, zone picking, or wave picking, has its own unique advantages, technical requirements, and potential drawbacks. The optimal choice depends on various factors such as the nature of the products, the volume and frequency of orders, available technologies, and the warehouse’s operational strategy.
By comprehending these methods and aligning them with specific operational needs, warehouses can significantly enhance order accuracy, increase productivity, reduce operational costs, and ultimately deliver superior customer satisfaction. As the warehousing landscape continues to evolve with advancements like robotics and automation, the exploration and integration of innovative order picking systems remain a key strategic priority for warehouses aiming to maintain a competitive advantage in this fast-paced industry.