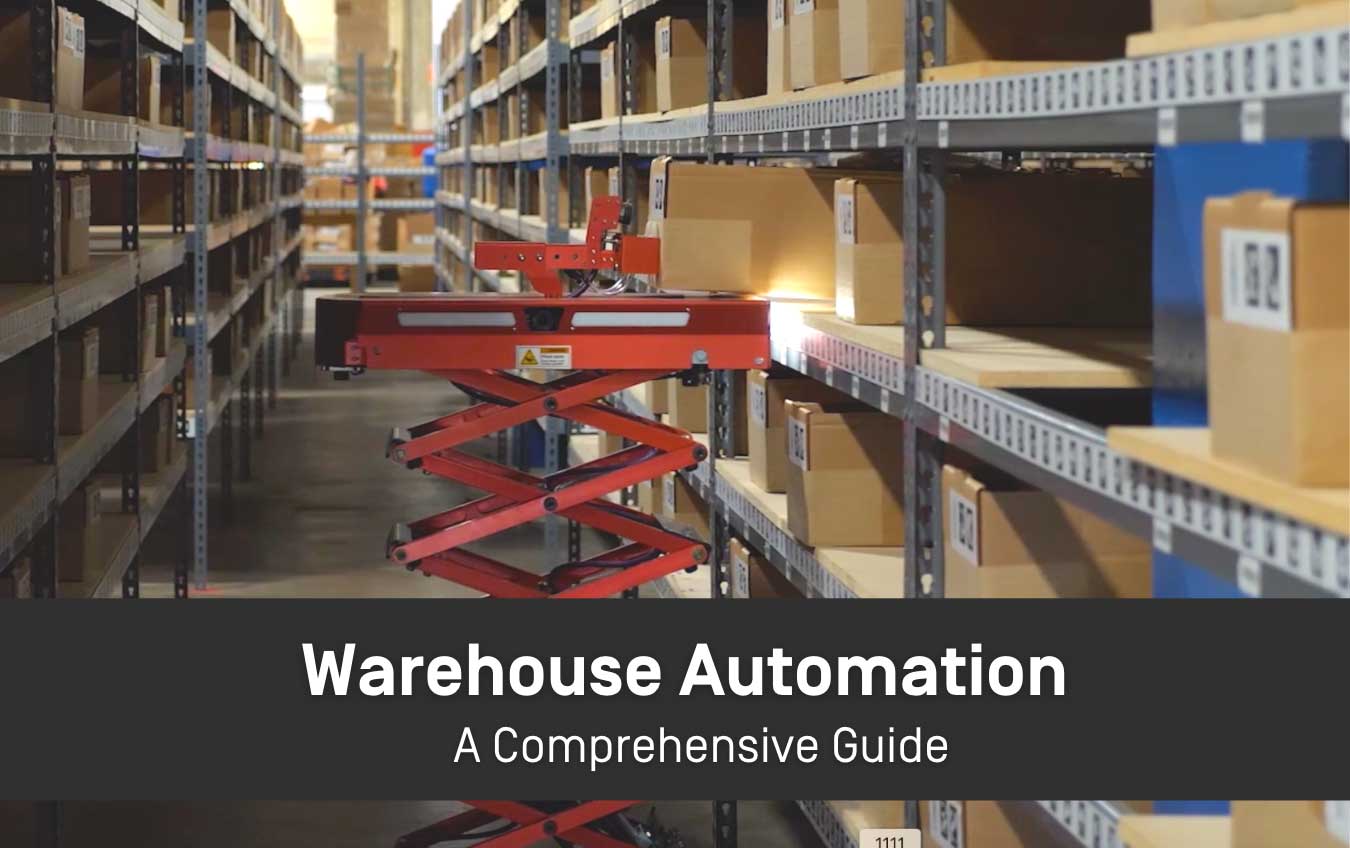
Table of contents:
- What is warehouse automation?
- Understanding warehouse software & robotic automation
- Types of warehouse automation used in E-commerce fulfillment
- Challenges and Considerations
> Order Picking Automation
> Adjusting Picking and Replenishment Workflows
> Packing automation
> Replenishment
> Loading and Unloading
> Palletizing
E-commerce has revolutionized the way consumers purchase and receive goods. Warehouse automation, once a niche concept, has now become a driving force behind the success of a supply chain. As a warehouse manager, you already know that logistics operations have to be agile and innovative to keep up. To keep pace with the ever-growing expectations for rapid order fulfillment, warehouse automation must be part of your overall supply chain strategy.
This article explores automation options for every step involved in fulfilling orders. Let’s examine workflows within warehouses and fulfillment centers and see how automation improves their speed and efficiency.
First, what is warehouse automation?
Warehouse automation refers to using technology to automate tasks and processes in a warehouse or distribution center. By integrating cutting-edge technologies such as robotics, artificial intelligence (AI), and data analytics, automation makes warehouses and fulfillment centers work better and faster.
Warehouse automation can encompass a wide range of functions, including inventory management, picking and packing, sorting, loading, and unloading, and even transportation within the warehouse. It optimizes operations, reduces manual labor, and enhances productivity.
Understanding warehouse software & robotic automation
Warehouse automation technologies do not necessarily involve machines or robots. They can also mean using software to streamline fulfillment, optimize manual tasks, and lower operating costs.
Robotic warehouse automation is when machines help move products and perform repetitive tasks such as material handling and order picking.
Software warehouse automation, on the other hand, uses software to plan, optimize and execute fulfillment tasks such as inventory management, order processing, and shipping. Warehouse Execution Systems (WES) software incorporates advanced technology, including artificial intelligence (AI), that helps orchestrate and coordinate all of the resources and tasks in a warehouse. The WES integrates with and extends the capabilities of existing warehouse systems, including warehouse management systems (WMS).
inVia Picker Robots, inVia Logic’s Warehouse Execution Systems (WES) software
Today, software-only automation systems alone can improve warehouse productivity, reduce operational costs, and make warehouse management easier and more efficient.
Types of warehouse automation used in E-commerce fulfillment
-
Order Picking Automation
Picking products off shelves to assemble an order is one of the most labor-intensive tasks in modern warehousing. E-commerce makes these manual processes even more demanding. The small number of products per order combined with a large variety of SKUs makes eCommerce order picking all the more challenging. There is a wide variety of robotic systems that fulfillment and distribution centers can choose today to automate order picking, most common include:
– Autonomous Mobile Robots (AMRs)
Autonomous Mobile Robots (AMRs) burst onto the warehouse automation scene within the last decade, and have quickly risen to become a driving force in improving eCommerce order-picking productivity. Currently, there are many mobile robotic picking systems available that can support both Goods-to-Person (GTP) and Person-to-Goods (PTG) picking methods. These systems can improve productivity by 2 to 5 times or more than traditional picking methods.
inVia Robotics uses a unique “Goods-to-Person” automation approach, where inVia Picker robots navigate the warehouse and autonomously remove inventory containers from the racks and deliver them to the inVia PickerWall, a dynamic high-density pick/put. The system decouples dependencies between people and robots, allowing people to work in bursts, while robots operate tirelessly 24/7. This highly efficient system can deliver 10x increase in picking productivity. (Read SICK Sensor Intelligence case study to learn more.)
– Fixed Automation
Automated Storage and Retrieval Systems (AS/RS) are large, fixed systems that use robotic cranes or shuttle conveyors to move products to and from storage. They deliver high productivity rates but are expensive and require considerable investment in infrastructure.
Interested in discovering more about robotic picking? Check out our blog post titled “Robotic Picking Systems: What You Need to Know.”
Robotic sorters take on many forms and have been designed to accommodate small packages, polybags, and padded envelopes and include a variety of solutions. One of the most common automated sorting systems employs AMRs with tilting trays mounted on top to move products from a conveyor system to a destination. The AMRs dump the products by tipping their tray and then return to the conveyor system for another load. The above-described system is merely one of many possible sorting solutions involving robots.
Packaging automation is not new, but novel capabilities have emerged as technology has developed. Automated labeling systems using lasers or inkjets, computer vision, special conveyors that can flip a package or turn it 90 degrees, and automatic insertion of primary packaging into secondary or shipping containers are all examples of modern packing automation. A robotic arm is now often employed at the end of an E-commerce conveyor system to lift products off of the moving belt and place them into boxes or shipping containers.
New automation solutions can now open boxes, decant products, and move them to their storage locations. However, the crucial element in automating replenishment lies in using automation software to control inventory levels dynamically, easily localize SKUs, and improve accuracy by minimizing human error.
An automated replenishment system monitors inventory levels and triggers replenishment workflows when product quantities fall below a predetermined threshold. For example, inVia Logic WES software analyzes key metrics and intelligently schedules inventory movement from reserve to primary pick locations. It aligns picking and replenishment tasks to avoid work stoppages or delays and ensures timely order fulfillment. If inVia Picker robots are utilized, the system guides AMRs to transport the containers to the appropriate location.
The job of loading and unloading trucks is uninteresting and tiring. As a result, retaining labor for such tasks is difficult. Advancements in computer vision technology combined with autonomous mobile robots have made it possible to automate much of this work.
For E-commerce, freight tends to be in loose boxes rather than full pallets, making automating the task considerably more complex. Even so, systems now exist that employ robotic arms using suction grippers and computer vision to determine whether to grab a box from the top – or the front – based on where the package is in the stack.
Palletizing robots and automation systems are mature technology. Commonly, a robot arm is positioned at the end of a conveyor system. The robot lifts boxes or packages from the conveyor and places them onto a pallet. The pallet can be automatically shrink-wrapped and then conveyed away. When a loaded pallet is complete, the palletizing robot picks up a new pallet, places it into position for loading, and begins putting boxes onto it again.
Challenges and Considerations
Cost:
Warehouse automation can be expensive, so careful attention must be paid to calculating your return on investment. ROI is often calculated based on labor cost savings, but market share opportunity cost and cost avoidance (replacing entire software systems) should be considered as other factors.
Many automation consultants suggest starting with a relatively small automation system. Prove its effectiveness, and scale up the operation.
inVia customers often choose to implement inVia Logic WES modular software first to integrate with their Warehouse Management System to boost warehouse workers’ productivity, improve workflows and help automate existing tasks. As a next step, some customers add inVia’s autonomous mobile robots to automate tasks further and achieve even greater productivity gains.
Integrations:
A robotic automation system often requires a Warehouse Execution System (WES) that must interface with your existing software systems, including warehouse management systems (WMS), transportation management systems (TMS), and enterprise resource planning (ERP) systems. When considering your choice of automation vendor, this subject deserves thorough investigation and discussion.
Training and Change Management:
The evidence suggests that automation does not cause warehouses to reduce their workforce. In fact, studies indicate that companies that invest in warehouse automation grow faster than those that don’t and consequently end up hiring more people! That said, people’s jobs will change, and it is wise to consider that as part of your implementation plan.
Preparing your people as the implementation date draws near is essential to ensure good acceptance. Describing strategic goals, the training and transition plan, and ongoing support are also crucial considerations.
Conclusion
Automation has become a necessity for modern warehouses and E-commerce fulfillment. Customer expectations for much faster delivery can only be met with automation. As technology advances, companies can access more comprehensive automated solutions than ever – including mobile robots for order picking, specialized conveyor systems for loading and unloading trucks, and highly compact and efficient sorting systems for small packages.
Although the upfront implementation costs may be high, with careful planning and the proper support from experts such as engineers, integrators, and software providers, a rapid ROI can be achieved.
Ultimately, companies should thoroughly research suitable warehouse automation solutions for their business. The experts at inVia Robotics are happy to provide their recommendations for those considering launching an automation project.