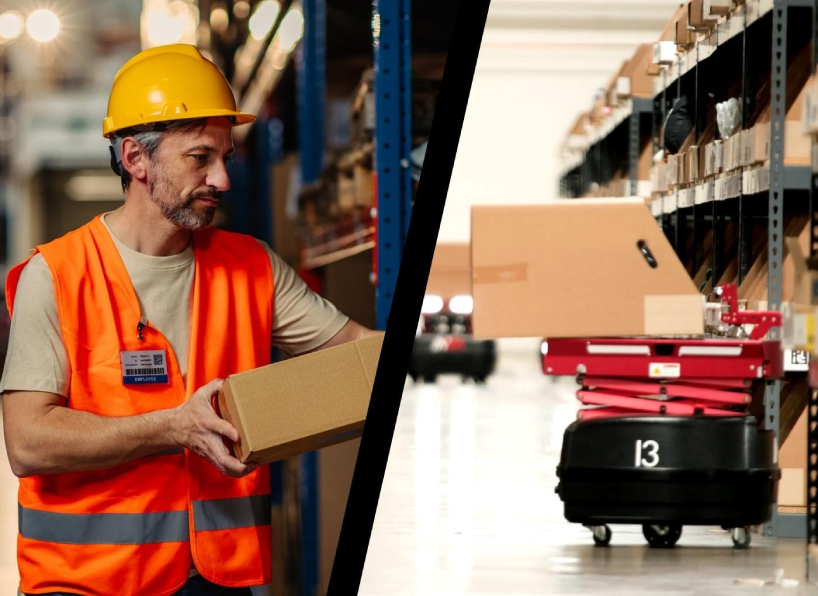
The need for greater automation to speed warehouse operations and meet consumer demand is having an impact on how warehouse workers spend their work time and perform their jobs. The emergence of smart warehouses which utilize the latest robotics capabilities working in concert with human workers rise a question about the future of people-robot collaboration. inVia CEO Lior Elazary addressed this topic and a range of others in a recent webinar, hosted by the Association for Advancing Automation.
Impact of Automation on Warehouse Workers
People work differently than robots. People tend to work in bursts, then take short breaks before re-engaging. Robots are better at working continuously, performing designated rote tasks over and over.
Warehouse automation is revolutionizing warehouses and distribution centers, improving productivity and efficiency. Whereas traditional warehouse workers might walk more than 10 miles each day picking and fulfilling orders across vast expanses of a warehouse floor, the use of robotics helps reduce workers’ inefficient travel time in the warehouse. This makes workers more productive, eliminates safety risks and reduces the physical and mental strains of extensive warehouse travels. Workers can assume more fulfilling and value-added jobs such as problem-solving when warehouse issues arise.
How do Warehouse Workers Feel About Automation?
In a recent survey reported by DC Velocity, 74% of on-floor warehouse workers said they would consider taking a pay cut at another company for an opportunity to use technology if it helps them in their jobs. Workers cited carrying and lifting, followed by walking and traveling, as the leading causes of physical strain that takes a toll on them. Technology can make a notable difference in addressing these job-related health challenges. For instance, inVia Logic proprietary algorithms determine the shortest and fastest routes significantly reducing the walking done each day by warehouse associates, helping lessen the chance for musculoskeletal issues. inVia PickMate’s pick-to-color productivity tools improve picking results by providing easy, step-by-step instructions.
According to an Accenture survey of warehouse workers reported by the Harvard Business Review, roughly 60% felt positive about warehouse automation. Workers were optimistic that automation would make their jobs safer, boost productivity and improve work quality. Those who were reluctant to automation worried they might lose their jobs, lack sufficient training and have to deal with downtime and errors caused by technology glitches.
One of the notable takeaways from the survey is that some workers felt that technology helps them improve performance and free them up for more interesting, less repetitive work. The survey findings have implications for how companies create growth opportunities for workers and train them to capitalize and succeed with these opportunities.
Did you know that it takes less than 30 min to train warehouse workers on inVia PickMate technology?
Common Myths About Warehouse Workers and Automation
There are a number of misconceptions about the impact that robotics and smarter warehouses may create:
— Myth 1. Robots Take Jobs Away
As noted earlier, autonomous mobile robots (AMRs) are most effective at performing rote, repetitive tasks while warehouse workers work most effectively in shorter, productive bursts. The use of robotics to create smarter warehouses should be viewed as additive not exclusionary. The most efficient automated warehouses have autonomous mobile robots and workers working in close collaboration on a division of labor aligned to their respective strengths to fully optimize their capabilities.
— Myth 2: Robots Create Safety Concerns
In truth, robots can actually help make warehouse environments safer for human workers. AMRs help sharply reduce the extensive walking that workers need to do in non-automated warehouses to perform picking, packing and fulfillment operations.
— Myth 3: AMRs Make Jobs More Difficult
On the contrary, robots and warehouse workers working in tandem can deliver significant gains in productivity and performance. inVia uses AI to continuously optimize the people and machines within a facility. AI learns the processes and patterns within a warehouse, then makes them more efficient to ensure robots and workers are fully optimized. inVia’s PickerWall solution creates a picking wall that provides a buffer between robots and warehouse workers so that each group can work in their designated areas to complete assigned tasks and work in concert.
The inVia PickerWall is designed to play to the respective strengths of warehouse workers and AMRs and realize an optimal use of labor. inVia PickerWall is a dynamic pick wall which inVia’s AMRs rebuild with each day’s new set of ordered goods. Robots are able to work in rote fashion non-stop on one side of the wall, while people can work in customary bursts on the other side of the wall to pull products and sort into order bins for pack out. This workflow decouples robot/people dependencies, allowing workers and robots to work independently in a mode best suited to their strengths to realize a facility’s target order fulfillment goals.
inVia PickerWall
Benefits of Warehouse Robotics for Workers
— Reduce Physical and Mental Strain
The miles that warehouse workers walk each day up and down the aisles can exact a physical and mental toll on workers. The physical demands can create greater fall risks and increase the chance for repetitive stress injuries. Warehouse robotics reduces the mental strain on workers as order picking robots can assume the more stressful and dangerous tasks such as transporting inventory, lifting products and even retrieving goods from heights. Reduced strain on workers can increase morale and boost productivity, which creates a better work environment.
inVia Logic proprietary algorithms determine the shortest and fastest routes for people and robots, anticipating and avoiding potential overlap.
— Eliminate Menial, Repetitive Tasks
Allowing autonomous robots to take over the menial or arduous tasks within a facility enables workers to tackle more complex tasks and strategic needs, such as picking and retrieving items. AMRs are better suited for locating and moving items over long distances. Product movement in warehouses is a non-value added task and can be a significant drag on the supply chain. Automating the movement of multiple SKUs within a facility and assigning workers to handle more strategic jobs can greatly increase efficiency and productivity.
— Improve Safety
Robots are able to use solutions such as inVia Logic and inVia SmartPath to follow optimized, predetermined pathways in a warehouse. Using their environmental sensors, AMRs can detect obstacles and adapt their movements accordingly. Workers walking miles each day across the warehouse can be distracted while carrying objects, which may lead to injuries from falls or collisions. Converting workers from pushing carts to picking and avoiding long travel makes them more productive and reduces safety risks within warehouses.
— Reduce Human Error
Increasing automation within a facility with a warehouse automation system can lower the potential for human errors. Warehouse robots locate and retrieve desired inventory, then return these items to a PickerWall, for selection and packing by warehouse workers. Reducing the number of human touches on an item limits the chances for human error.
To learn more about automated warehouses and how robots can co-exist with human workers please visit this on-demand webinar.