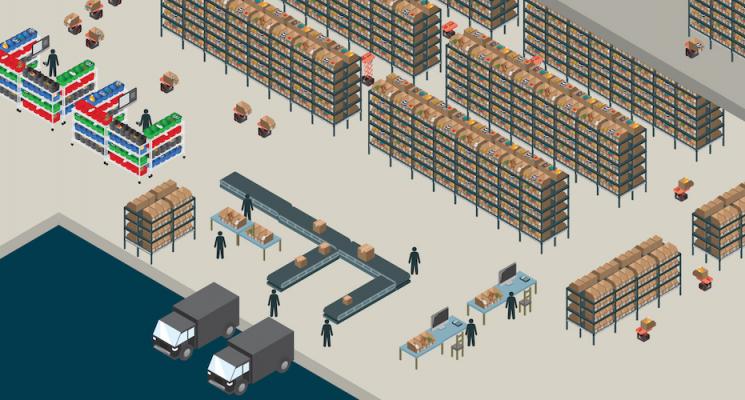
Online shoppers don’t care how their orders get assembled and shipped, they only care that they get the right items as fast as possible. Making sure those orders are filled accurately and leave the warehouse quickly requires a lot of work in the background that customers will never see—work that is being transformed by robotics and automation.
To better understand this transformation, let’s start with the basics.
Orders
When customers go onto a website and select the items they want to purchase, those items are added to an online shopping cart. Depending on the type of item, shoppers may also need to select sizes, colors, or quantity. For example, a customer buying three sweatshirts, three t-shirts, and one duffel bag will likely select a variety of sizes and colors in addition to quantity.
Once those items in the shopping cart are moved to checkout and the purchase is processed, that’s an order.
Lines
Lines are all the different items in the order, which fulfillment warehouses track by each item’s individual Stock Keeping Unit (SKU) or Universal Product Code (UPC).
Units
Units are the quantity of each line in the order, so in this scenario, we have:
- 1 order
- 3 lines
- 7 units
Getting the items from the warehouse shelves to the area where they are packed and shipped is the job of a picker, and a picker’s level of productivity is one of the key metrics that warehouse managers evaluate to measure efficiency.
Many managers look at the number of units a worker picks in an hour (UPH) as the standard measure of throughput, while some prefer to track lines per hour (LPH), depending on which picking method they are using.
And while these numbers are useful in monitoring KPIs and performance-based incentives, they can often be misleading. The number of units a picker retrieves in an hour may not take accuracy into account, and every time an item is missed or the wrong one is picked, it creates a ripple effect of lost time while the order is being fixed.
In order to get a true picture of productivity, you need to be looking at a comprehensive, data-driven warehouse automation solution that can uncover inefficiencies and recommend process improvements. And that’s where we come in.
Investing in Robotics and Automation
inVia’s Robotics’ automated picking system is much more than just robots—it’s an AI-powered software system that integrates seamlessly with any Warehouse Management System (WMS), allowing you to monitor your operations and make informed decisions.
Our system establishes a baseline that lets you see how productive your people are. It then provides real-time metrics that track your overall productivity once robots are integrated into the fulfillment process. Additionally, we provide metrics on order fulfillment accuracy, so you can see the true cost of running your operations. Business intelligence reports are included that examine your processes from numerous angles, giving you the ability to leverage a comprehensive set of data points to introduce greater efficiency across your warehouse.
You can track UPH and LPH, monitor individuals or groups, compare throughput levels of robots and people, and make changes in real-time.
Why Does It Matter?
Having the ability to input, capture and manage data on so many levels provides a much more accurate and holistic view of warehouse productivity, allowing you to fine-tune your operations for maximum efficiency.
Ready to put the power of mobile robotics to work in your warehouse? Please give us a call – we’d love to hear from you.