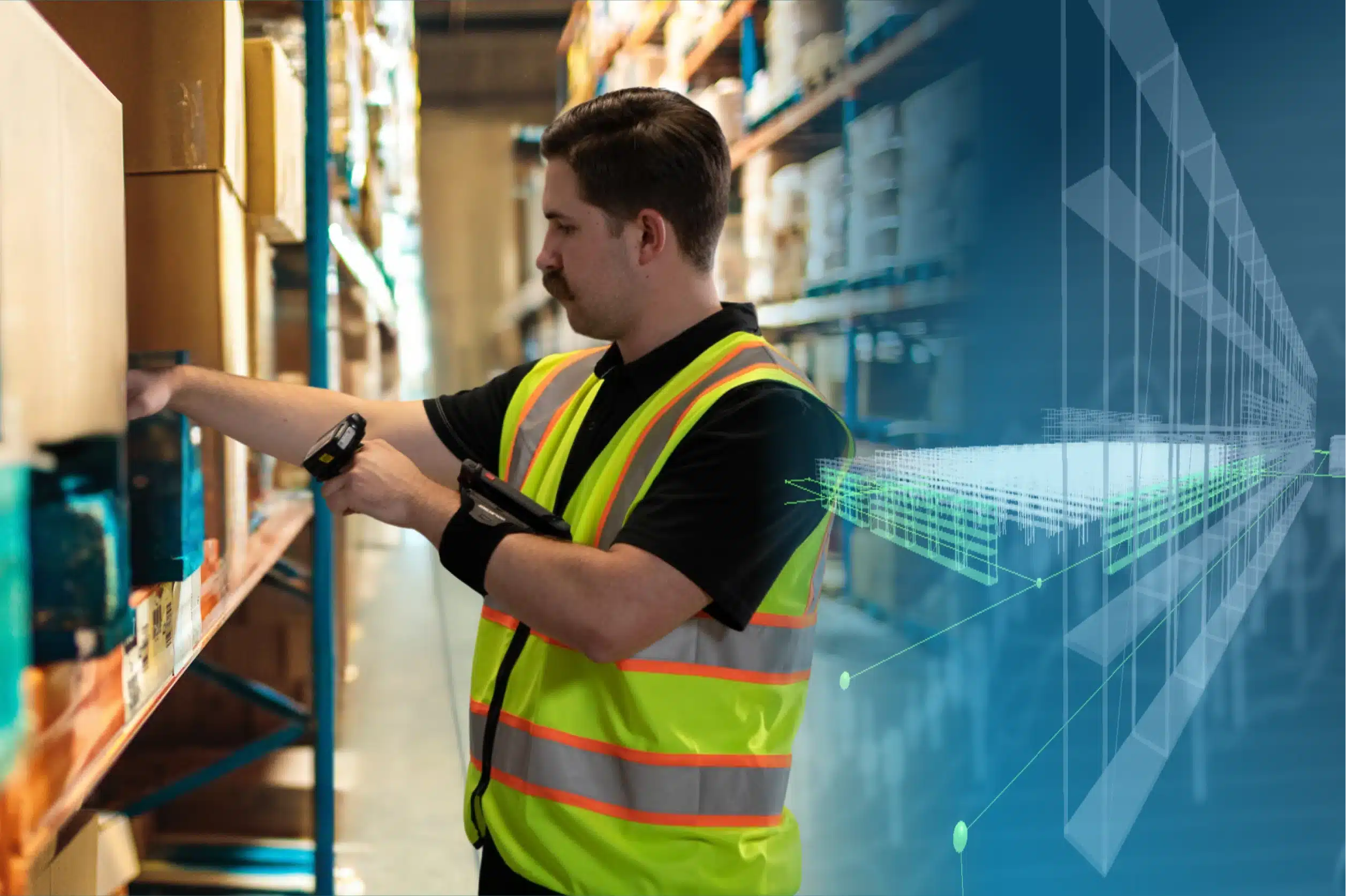
Over the years, companies have explored various strategies to improve picking speed and efficiency in their warehouses. From zone picking, where workers are assigned specific areas, to batch and cluster picking, which involve handling multiple orders at once, businesses have tried it all. Yet, wave picking remains the most popular approach today. Wave picking organizes orders into scheduled batches (waves), offering some control over workflows but also leading to downtime and bottlenecks.
As fulfillment demands grow and real-time adaptability becomes essential, waveless picking emerges as the next step in warehouse optimization. Waveless picking keeps operations moving continuously, providing a faster and more flexible solution.
What is Wave Picking vs. Waveless Picking?
Warehouse managers face thousands of orders, inventories, and potential problems daily. They must decide which orders to prioritize, what can wait, and how to fix issues like shortpicks or delays. To manage this complexity, businesses developed wave systems. These systems batch orders into waves based on shared characteristics like delivery routes or carrier schedules.
Wave systems help manage large volumes of orders. However, once a wave is set, adjusting for rush orders or issues like shortpicked items becomes difficult, leaving little time to fix problems before shipping deadlines. This rigidity leads to inefficiencies, such as downtime between waves and missed opportunities to meet delivery expectations.
Waveless picking processes orders individually and dynamically prioritizes them based on factors like Service Level Agreements (SLAs), shipping deadlines, and real-time conditions in the warehouse. Any issues, such as shortpicks, are identified and addressed immediately, allowing for more efficient and flexible order fulfillment.
- The black line represents wave picking, where productivity peaks during batch processing and drops off sharply due to periods of inactivity between waves.
- The yellow line represents waveless picking, where productivity remains stable because orders are continuously fed into the system, keeping workers and robots constantly moving.
This graph highlights the primary advantage of waveless picking: smoother, more consistent operations. While wave picking leads to spikes and drops in productivity, waveless picking ensures a steady flow of work, allowing warehouses to operate efficiently throughout the day
How Waveless Picking Works and How inVia Makes It Possible
Waveless picking allows orders to be processed individually in real time, but achieving this level of efficiency requires intelligent resource management. This is where inVia’s AI-powered Warehouse Execution System (WES) comes in. By using advanced AI to quickly process large amounts of data, inVia Logic WES manages each order separately, factoring in Service Level Agreements (SLAs), shipping deadlines, and what’s happening in the warehouse at any given moment.
- Data Gathering and Learning: inVia Logic first collects extensive data from the Warehouse Management System (WMS), including order details, inventory levels, and SLAs. But it doesn’t stop there—it also learns about the available resources in the warehouse, such as the number of workers and robots, and factors in individual behaviors like travel speeds and picking rates. This gives inVia Logic a clear picture of the current conditions in your warehouse each day.
- Smart Decision-Making: Unlike systems that rely solely on basic productivity metrics like Units Per Hour (UPH), inVia Logic considers the complexity of tasks, such as handling larger items or navigating across different warehouse zones. This allows inVia Logic to predict worker behavior and make smarter decisions that optimize the workflow.
- Real-Time Optimization and Task Assignment: With AI driving the decisions, inVia Logic constantly monitors warehouse activity and adjusts tasks in real time. As conditions change—whether due to a surge in orders or a resource shortage—the system instantly reprioritizes tasks, ensuring that workers and robots stay focused on the most efficient routes and tasks.
- Seamless Automation: inVia’s WES seamlessly coordinates robots and workers, ensuring a smooth flow of operations. If there’s a shortpick or a high-priority order, the system makes quick adjustments to keep everything running without disruption.
The real power of inVia’s WES lies in its ability to continuously monitor, analyze, and fine-tune workflows. It doesn’t just react to problems—it anticipates them, adjusting task assignments to keep every order moving efficiently. This ongoing cycle of real-time optimization helps warehouses run smarter, faster, and with more flexibility than wave-based systems ever could.
By switching from rigid wave-based systems to a waveless approach, warehouses can unlock a new level of efficiency and flexibility. Waveless picking, powered by AI-driven systems like inVia Logic WES, eliminates downtime, responds to issues in real time, and keeps orders flowing smoothly. This continuous operation means higher productivity, better resource utilization, and the ability to adapt to today’s fast-paced fulfillment demands. As the industry continues to evolve, waveless picking isn’t just an upgrade—it’s the future of warehouse optimization.