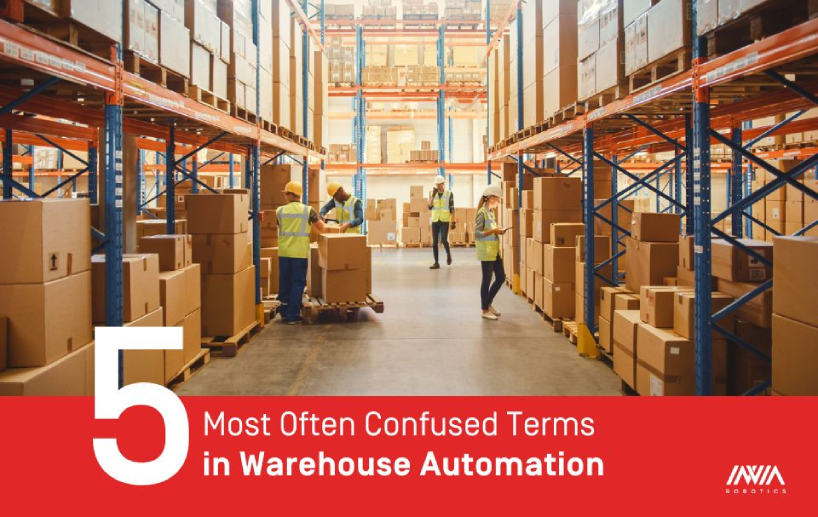
With the rise of customer demand for online shopping, warehouses and all nodes of the supply chain are feeling pressure to reduce delivery times. Robotics providers are responding with innovative ideas and creative solutions. Warehouse automation has entered a revolutionary new phase. However, as the new solutions continue to reshape the warehouses and distribution centers, familiar terms take on a new meaning while new warehouse automation terminology is introduced. Warehouse industry definitions that made sense in the past may not perfectly fit the new procedures and workflows.
In this article, we explore five of the most often confused warehouse automation terms.
1. Person-to-Goods (PTG) vs Goods-to-Person (GTP) Automation
There are many types of warehouse automation solutions that distribution operations can choose today. Most fall under two categories: Person-to-Goods (PTG) and Goods-to-Person (GTP) automation.
With both GTP (Goods To Person) and PTG automation, the goal is to increase order-picking efficiency and minimize warehouse walking. For warehouse automation, walking is the adversary because it is a low-value activity detracting from the number of orders that can be picked per hour. Studies show warehouse associates spend as much as 50% of their time walking during the order-picking process.
Traditional Person-to-Goods (PTG) Order Picking. Source: istock
Goods-to-Person (GTP) order-picking automation, on the other hand, reduces walking (even more than P2G) by bringing products to a (mostly) stationary person. One example of GTP automation is a “Rack-to-Person” method. Low-profile, order picking robots go underneath an entire shelf of goods, lift up the shelving unit and carry it to an order-picking station. Associates see a display indicating the items to pick and the bins where they’re stowed.
The disadvantage to a racks-to-person approach is that humans and machines often work at different paces. Racks and goods can pile up while an associate takes a break. During peak periods, robots may bring more racks to the order-picking station than the people can handle, and again, the result is a bottleneck.
inVia avoids these bottlenecks with a patented approach that can be described as “Totes-to-Person” or more specifically “Totes-to-PickerWall”. inVia Picker robots travel to the appropriate warehouse location and autonomously remove a tote from the shelf using a suction cup mechanism. A scissors lift enables the robot to reach up to high shelves. The robot brings the tote to an inVia PickerWall, where associates pick items from the totes, directed by displays and pick-to-light prompts. The associate travels very little – from one end of the PickerWall to the other at the most – a few dozen feet.
The crucial advantage of the inVia system is that it decouples human and robotic processes. The associates can pick orders in spurts – appropriate for humans – and the robots can work methodically 24/7 – as robots can uniquely do. The result is to eliminate the bottlenecks seen with other approaches.
2. What are Cobots: Robot Arm or Smart Cart?
Collaborative robots or “cobots” are a relatively new development. The term has been primarily used for collaborative robotic arms, although more recently, the term Cobots has been used to describe smart carts or Person-To-Goods autonomous mobile robots in distribution centers.
Starting already in the 1950s, automobile makers were the first to adopt robot arms as part of their manufacturing process. These early, “non-collaborative” robots picked up engines and car frames and rapidly moved them around. They were large and powerful, and if you got in their way, you could become seriously hurt, or even killed. Consequently, these robot arms were caged off from the employees, and only specially trained people were allowed to go inside the fenced-in work cell with the robots.
Some fifteen years ago, a new variety of robotic arms was introduced that could work alongside people. These cobots had built-in sensors so they would automatically slow down or stop if a person came near. Cobot arms evolved to include bump detection so that even if they did collide with a person, the robot would immediately stop and reverse itself to limit or avoid damage. More and more features continue to be introduced to make cobot arms safer and easier to use.
Soon after, robotic smart carts began to be introduced onto factory and warehouse floors. They are often referred to as “Cobots” because they can detect the presence of people and slow down, stop, or swerve to avoid a collision. They also collaborate with people, aiding in order picking.
So, what is a cobot? In strict terms, Cobot refers to the collaborative robot arm. However, technically, any robot that is designed to be safe around people and to collaborate with them can be called a cobot. Robots are increasingly used side-by-side with people to assist them with tasks. With a broader application, we can expect this term to continue to take on new meanings.
3. AMRs vs AGVs Robotic Solutions
These two terms cause a lot of confusion because there is ambiguity about the differences between them. Both AGVs (Automated Guide Vehicles) and AMRs (Autonomous Mobile Robots) are driverless, smart vehicles that transport items within a facility.
AGVs travel along predetermined paths as prescribed by guides in the floor or markers on walls and shelves. If an obstacle blocks their way, they cannot navigate around it. The AGV simply stops and calls for help. AGVs tend to be used to carry more massive objects like pallets of goods and jet engines.
AMRs carry a stored map of a facility in their memory and can independently navigate from one point to another. In Goods-to-Person automation, such as inVia Robotics, AMRs move completely autonomously to automate all order fulfillment tasks. Smart algorithms calculate the most efficient paths for robots to retrieve and move goods to warehouse workers so that they can quickly pick, scan, and sort items for packing and shipping to customers. If an obstacle blocks its way, an AMR can autonomously take a different route to its assigned destination. AMRs tend to carry somewhat smaller cargo than AGVs – like totes or bins.
Now that these differences have been noted, the two types of devices are tending to converge. AMRs are becoming larger and more capable of handling massive loads, and AGVs are growing smarter.
Still, AGVs and AMRs have quite different applications for warehouse operations. The AGVs are most often used for larger, heavier payloads, that need to be moved along the same defined path. AMRs are much more flexible and are optimally used for order picking, replenishment, and transporting boxes rather than large objects.
4. WMS software vs WES software
A warehouse management system (WMS) is a type of software that provides inventory management and tracks all materials and goods as they come in and go out of the warehouse. Warehouse processes and procedures employed in the 19th and 20th centuries that used paper and pencil were simplified forms of warehouse management systems. With the rise of computing power, they were replaced by electronic spreadsheets.
The modern use of the term WMS refers to the computer software that keeps track of inventory and where things are in the facility. Not all WMS software is created equal, and some is more complex and sophisticated than others, but generally, a WMS is used maintain the records of the inventory.
Warehouse Execution Systems are a more recent development. WES software was designed with automation in mind. While WES can encompass many of the WMS functions, it can also control robots, conveyor belts, packaging machines and other types of equipment.
Many warehouses have a WMS that they’ve used for a decade or more. Although warehouse management may find robotic automation to be attractive, the idea of scrapping their WMS – which is often highly customized – is an intimidating prospect. This is why many warehouse automation systems are designed so that the WES can interface with the existing WMS. Automation can be introduced without the need to completely do away with the WMS.
So the WMS and the WES work together.
The inVia Logic WES software is designed to easily integrate with the existing WMS systems, so you can get the productivity increase from modern automation without the hassle of completely revamping your software. While existing WMS “manages” the warehouse inventory, inVia Logic WEX “executes” the physical movement of that inventory.
5. Pick-To-Light vs Pick-To-Color
Picking strategies and technologies are critical to boosting distribution centers’ productivity. Order picking accounts for more than 50% of warehouse operating costs and more than 55% of fulfillment center operations.
The two order picking technologies we’d like to highlight are Pick-to-Light and inVia’s patented Pick-to-Color technology to understand the benefits and key differences with each system.
Pick-to-light is an order fulfillment technology for warehouses and distribution centers that uses alphanumeric display lights and buttons at selected locations within facilities to guide manual picking and record orders for shipment. Warehouse workers scan barcodes attached to holding containers.
inVia has developed a unique Pick-to-Color solution that uses AI-guided software to speed up order processing and accuracy in the warehouse. While inVia Logic software uses AI to optimize the placement and movement of goods, inVia’s PickMate warehouse order picking tool guides workers to use the intelligence that inVia Logic creates. Employees are able to simply match the color on the screen with the color on the inventory. This warehouse order-picking technology makes it easy to identify the right SKUs in the right locations. Simple visual cues make picking and placing simple and intuitive.